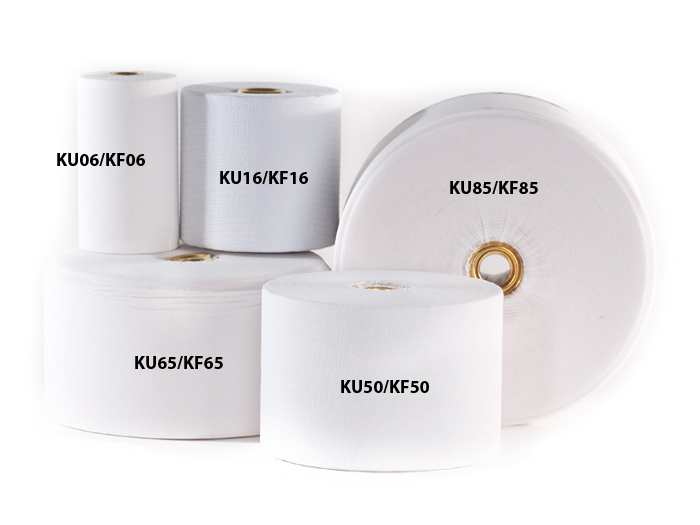
The Kleenoil Filter Cartridge is made of densely wound, pure coniferous long fiber wood pulp. It is held together in a material casing and comes in specified sizes for use in the appropriate filtration units as shown in the specification table below.
The action of the cartridge: The filtration cartridge acts by both absorption and adsorption in a continuous recycling process. The long fibers of the paper attract the water formed either through the combustion process or by condensation and absorb it like a sponge. At the same time, it rejects the larger, oil molecules which are forced to pass between the tight windings of the cartridge. As the oil passes through the cartridge, minute carbon, wear metal, and silicon particles are extracted from the oil and adhere to the many surfaces of the filter – a process known as adsorption. Thus, by removing water, the cartridge inhibits the production of acids which both degrade the oil and cause excessive wear. The simultaneous removal of minute contaminants as they occur enables the oil life to be extended within [beyond?] its original operating specifications.
The Kleenoil Filter Cartridge removes particles down to 1 micron and eliminates water. The principle for filtering particulate matter is “liquid chromatography”. In effect, this principle allows fluid to drain down a surface that progressively arrests the particles. Oil passes up the core of the paper roll where it collects in a cavity between the lid of the filter housing and the paper roll. The oil is then forced down between the layers of tissue where particles are adsorbed within the matrix created by millions of cellulose fibers that form the tissue layer.
The principle for filtering water is “capillary absorption” into the hollow vegetable fibers of the cellulose tissue. The molecular structure of the oil, however, is too large to be absorbed into the fibers, but water is absorbed and separated from the oil.
The Kleenoil Filter Cartridge is made of cellulose tissue (paper), and we always use a long fiber tissue that has not been previously processed. Most papers are made with a large amount of re-pulped material, and, as a general rule, the fiber length is roughly halved each time the paper is re-pulped. Short fibers will absorb water, but the pressure of flowing oil will cause the water to be released back into the oil. A long fiber, on the other hand, will have its ends crushed by the pressure of the oil flow, and a small portion of water will be permanently retained in each fiber. Water retention is approximately 2.2 liters per kilogram of tissue.
Furthermore, to be able to retain a large amount of very small particles, the winding of the cellulose roll must be extremely precise. Normal paper converters operate at high speed, and the motion is not particularly smooth. To make an efficient filter, the winding must reflect constant and even tension, yet not be so tight that oil will not flow freely. Re-pulped tissue with shorter fibers does not have the tensile strength to permit the tension without breaking.
As such, the cellulose tissue used to manufacture a Kleenoil Filter Cartridge must be from virgin coniferous or other long fiber wood. It must not have any re-pulped material. There must be no chemicals such as optical bleach present as this could alter the features of other chemicals added to the oil. There must also be a constant, slow wind to give the optimum density and tension to the material.
Any proprietary tissue would be unlikely to produce a filter that would meet the established specification of filtration to below 3 microns and total water removal within five passes.
Important Note: While the Kleenoil Filtration Unit does extract water and contaminants, it also continuously safeguards the desirable elements compounded within the oil in use. Dependent on use, these typically include dispersants, detergents, oxidation and rust inhibitors, metal de-activators, pour-point depressants, viscosity improvers, lubricity agents, fungicidal agents, and anti-foaming and gelling additives. These additives are held in suspension, and their levels can be critical if the oil is to maintain its beneficial qualities.
Oil Flow Rate: Output levels are dependent on viscosity, temperature, degree of contamination, and oil pressure. Guidelines: For SAE, 15w/40 oil @ c/ 60PSI/ 0.44gcm/ 2.0Lmp / 95°C
Operating Temperatures: Within the operating specifications of the engine, gear, and hydraulic oils. Filtration Level: Particulate contamination in accordance with BS 5540 part 4: 1981 and ISO/DIS 4406. ISO is equivalent to NAS 1638 class 6 (hydraulic oil specification).